Design Engineering Theory Topics - Home Page |
Manufacturing Processes
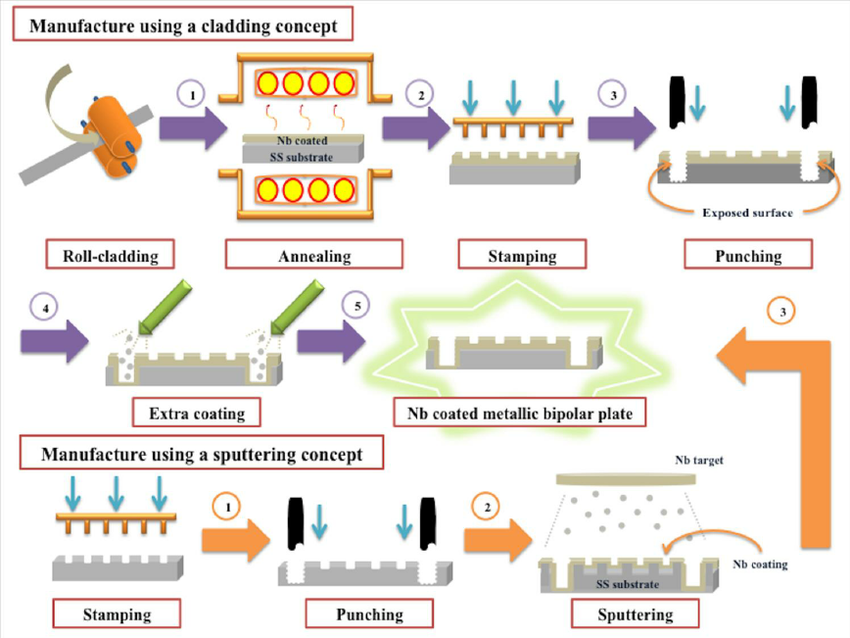
1 Processes
- Manufacturing engineering or manufacturing process are the steps through which raw materials are transformed into a final product. The manufacturing process begins with the product design, and materials specification from which the product is made.
Photo etching
- Photo etching is the method of producing a printed circuit board (PCB).
- The process is a follows:
- Print the PCB design onto a clear transparency sheet using a laser printer.
- Cut the PCB to size.
- Peel the sticker (protective blue layer) from the PCB.
- Place the exposed photo-board on top of the laser printed design inside a UV light box.
- Allow the PCB to be exposed for the required length of time. Ours takes 4 minutes.
- The board now goes into the developer tank which removes the now softened PCB protection layer.
- The PCB then goes into the ferric chloride tank to remove the excess copper.
- The PCB is then sprayed with photo-resist stripper to remove the final layer of protective film on the PCB.
- This is the best process for making PCBs in schools.
- It is however, a vey slow process and not suitable for mass production.
- All the chemicals need need regular replacement as they become saturated with copper.
- These chemicals will need to be disposed of safely.
PCB population
- Once the etching process has been completed, the PCB will need to be prepared and populated with components.
- The PCB will need to be drilled using the appropriate size drill bit, usually 1mm, this will be slightly bigger for components with thicker legs. 1.5mm for the download sockets.
- Components are then pushed through the holes and then soldered in place on the opposite side where the copper tracks are.
- You must ensure all the holes are drilled before placing components, as it is usually very difficult to drill holes after the components are placed.
2 Scales of production
- When you decide to manufacture a product it is important to choose the correct scale. Smaller production numbers will a require very different process compared to large scale production.
- The method you choose to produce your design will have a significant impact on the cost to produce it as well as the setup costs.
One-off prototyping
- When you wish to produce a circuit as a prototype to test it before full scale production, one of the methods that can be used is 'breadboarding'.
- A breadboard also known as protoboard is a type of solderless electronic circuit building.You can build a electronic circuit on a breadboard without any soldering! Best of all it is reusable.
Batch
- When you need to produce a number of the same product at the same time, a single batch production might be used.
- For this process, jigs (fits over a piece of material to guide accurate cutting or drilling without the need for marking) or templates (a cut-out of a shape that can be drawn around onto the material to mark out quickly and easily) are used.
- A good example of this is vacuum forming. This is a system which uses a mould to produce the same shape repetitively.
- Advantages:
- The jigs and templates speed up the process and can be kept for future use.
- There is no need for expensive specialist equipment.
- increased production efficiency by reducing setup time
- improved accuracy and consistency of parts through precise workpiece positioning
- decreased labor costs by simplifying operations
- reduced scrap rates due to better quality control
- the ability to produce identical, interchangeable parts
- Disadvantages:
- Very labour intensive using the jigs and templates.
- Producting the jigs and templates can be costly
- significant setup time
- limited flexibility for different workpieces
- the need for careful maintenance and storage
- potential limitations in adapting to slight variations in material thickness or design
Mass Production
- When you wish to produce a product large scale (in the thousands), you will need to use a mass production method.
- These are the processes you will usually find in factories.
- Mass-produced metal products include door handles, barbecues and cooking utensils.
- The setup costs for these factories is very high, but as you will be producing thousands of the product, the cost should be offset against this.
- Examples of mass production processes are:
- Injection moulding.
- Blow moulding.
- Stamping.
- Advantage:
- Can make products very quickly.
- Significantly lower production costs due to economies of scale
- Increased efficiency through automation
- Standardised product quality
- Reduce labour costs
- Disadvantages:
- Very expensive to setup
- Only cost effective if large numbers are made and sold
- Employees who remain part of an assembly line may lack motivation because their tasks are repetitive. The boredom caused by repetitive work can lead to low employee morale and increased levels of turnover.
-
Resource depletion - Mass production uses large amounts of resources, which can lead to resource depletion.
-
Pollution - The manufacturing processes and materials used in mass production can cause air and water pollution.
Injection moulding:
Blow moulding:
Stamping:
Continuous
- This is the next step from mass production but the process runs 24 hours a day.
- This process is used when very high volumes are needed and the factory can not be shut down over night.
- When the process is very long and stopping and starting it can cause serious delay then this process is used.
- A good example of this is the car industry. If any stage in the production line is stopped delays and backups are created in other parts of the line.
- Advantage:
- Makes larger numbers of products very cheaply and quickly.
- Increased production rate: Continuous production can run 24/7, allowing factories to produce large quantities of goods.
-
-
- Disadvantages:
- Machinery is very expensive.
- Only worthwhile if very large numbers of the product are made and sold.
- Limited flexibility to change products
- Potential for overstocking
- High resource intensity due to always running machinery
- Increased risk of production disruptions if a single machine fails
- Lack of adaptability to changing market demands
3 Techniques for quantity production
Pick and place and surface mount technology
- This system is used when making PC boards.
- It is used to place components onto a PCB before heating them to solder the components.
- This is referred to as surface mount technology (SMT).
- Click on this link to read more about SMT technology.
Quality Control (QA)
- If you are to produce a product you do not want to make the entire product and then check to see if it works and is in good condition at the end.
- You will want to check at many points along the way to ensure the product or parts are up to standard before moving onto the next step.
- This is known as quality control (QA).
- You will want to setup as many points as you can in you production line to QA the product before moving onto the next step.
Marking out methods
- Measurements are taken from a baseline or datum surface. A lot of tasks require two datum surfaces at right angles to each other. Smoothing off will turn a rough, newly-sawn edge into a datum surface.
- To create a datum surface on wood, a plane is used.
- To create a datum surface on metal and plastics, a flat file or hand file is used.
- To read more about this, go to the BBC bitesize website.
Templates
- When turning a detailed shape, a card template is very useful.
- The template can be pushed against a material, in order to check the accuracy of the shape/form.
- It can also be used to draw a complex shape onto a material repeatedly.
- To learn more about templates, click on the link.
Patterns
- A pattern is used to make an exact copy.
- Dress makers use these to make dresses or clothing to an exact pattern.
Sub-assembly
- Complex machines are made up of many different parts or sub-assemblies.
- Often these sub-assemblies are made up at different locations and then sent to one factory to put the all together.
- For example, in the car industry, braking systems, electrical harnesses, and dashboard clusters are usually built and assembled at a plant and then are send to the car factory where they are put in the vehicle.
Working with tolerance
- All parts manufactured are never perfect.
- For example, most parts will expand and contract depending on their temperature. So when producing parts, you will need to take this into account and adjust your design to accomodate small changes.
- Other issues you might face is the measuring equipment is not always 100% accurate.
- Manufacturers always build in tolerances to allow for all these slight indifferences.
- These are usually indicated in a +/- value.
- For example, most of the resistors we use have a gold band at the end, this indicates there is a +/- 5% tolerance of the reisitors value in ohms.
- This can also be in +/- mm if size is the issue.
- Some industries will have a higher value tolerance the other, for example, in the building industry, tolerances of a few millimetres will be acceptable. Where the car industry tolerances will need to be within a few thousandths (0.001mm) of a millimetre!
Efficient cutting to minimise waste
- You will always need to consider the materials you use and try to ensure you use as much of it as possible to minimise waste.
- As the raw materials cost money this will save you money.
- For example, we use 600X300mm plywood sheets. When designing your product, you will need to try use as little of this material as possible. This is a process called nesting.
4 Practice Questions
Practice Questions
- What is a breadboard used for?
- What is a Jig?
- What is a template?
- Why does it make it cheaper to produce a product when using jigs and templates?
- Why do you need to consider tolerance in the designing of a part?
- What production method is best if you want to make 20 of the same product and why?
- What production method is best if you want to make 50 000 of the same product and why?